Los métodos de recubrimiento de fotoprotectores generalmente se dividen en recubrimiento por rotación, recubrimiento por inmersión y recubrimiento por rodillo, entre los cuales el recubrimiento por rotación es el más utilizado. Mediante recubrimiento por rotación, el fotorresistente se gotea sobre el sustrato y el sustrato se puede girar a alta velocidad para obtener una película fotorresistente. Después de eso, se puede obtener una película sólida calentándola en una placa caliente. El recubrimiento por rotación es adecuado para recubrir desde películas ultrafinas (aproximadamente 20 nm) hasta películas gruesas de aproximadamente 100 um. Sus características son buena uniformidad, espesor de película uniforme entre obleas, pocos defectos, etc., y se puede obtener una película con alto rendimiento de recubrimiento.
Proceso de recubrimiento por giro
Durante el recubrimiento por rotación, la velocidad de rotación principal del sustrato determina el espesor de la película del fotoprotector. La relación entre la velocidad de rotación y el espesor de la película es la siguiente:
Giro=kTn
En la fórmula, Spin es la velocidad de rotación; T es el espesor de la película; k y n son constantes.
Factores que afectan el proceso de recubrimiento por rotación.
Aunque el espesor de la película está determinado por la velocidad de rotación principal, también está relacionado con la temperatura ambiente, la humedad, la viscosidad del fotorresistente y el tipo de fotorresistente. En la Figura 1 se muestra una comparación de diferentes tipos de curvas de recubrimiento fotorresistente.
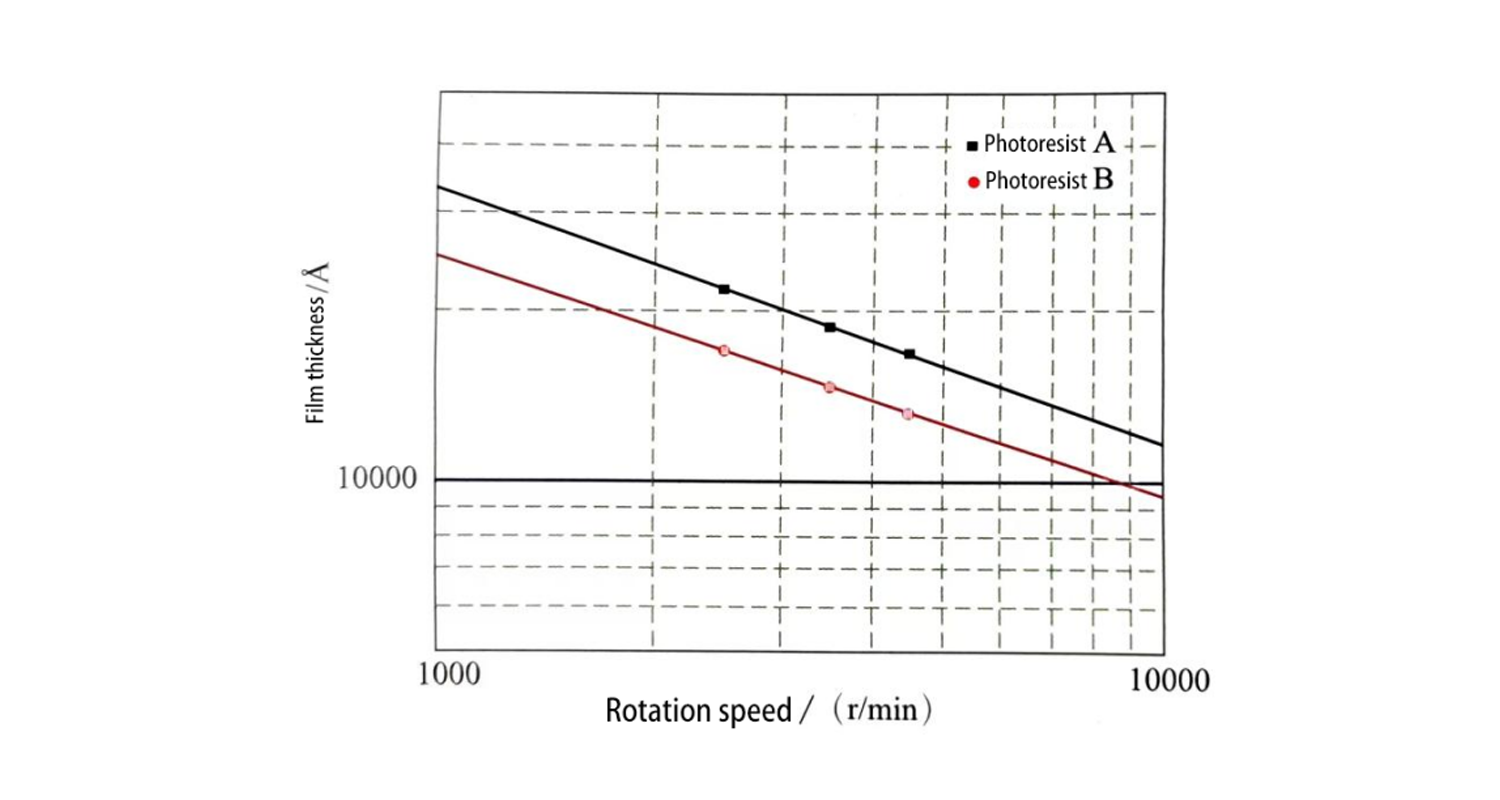
Figura 1: Comparación de diferentes tipos de curvas de recubrimiento fotorresistente
La influencia del tiempo de rotación principal.
Cuanto más corto sea el tiempo de rotación principal, mayor será el espesor de la película. Cuando aumenta el tiempo de rotación principal, más delgada se vuelve la película. Cuando supera los 20 s, el espesor de la película permanece casi sin cambios. Por lo tanto, el tiempo de rotación principal normalmente se selecciona para que sea superior a 20 segundos. La relación entre el tiempo de rotación principal y el espesor de la película se muestra en la Figura 2.
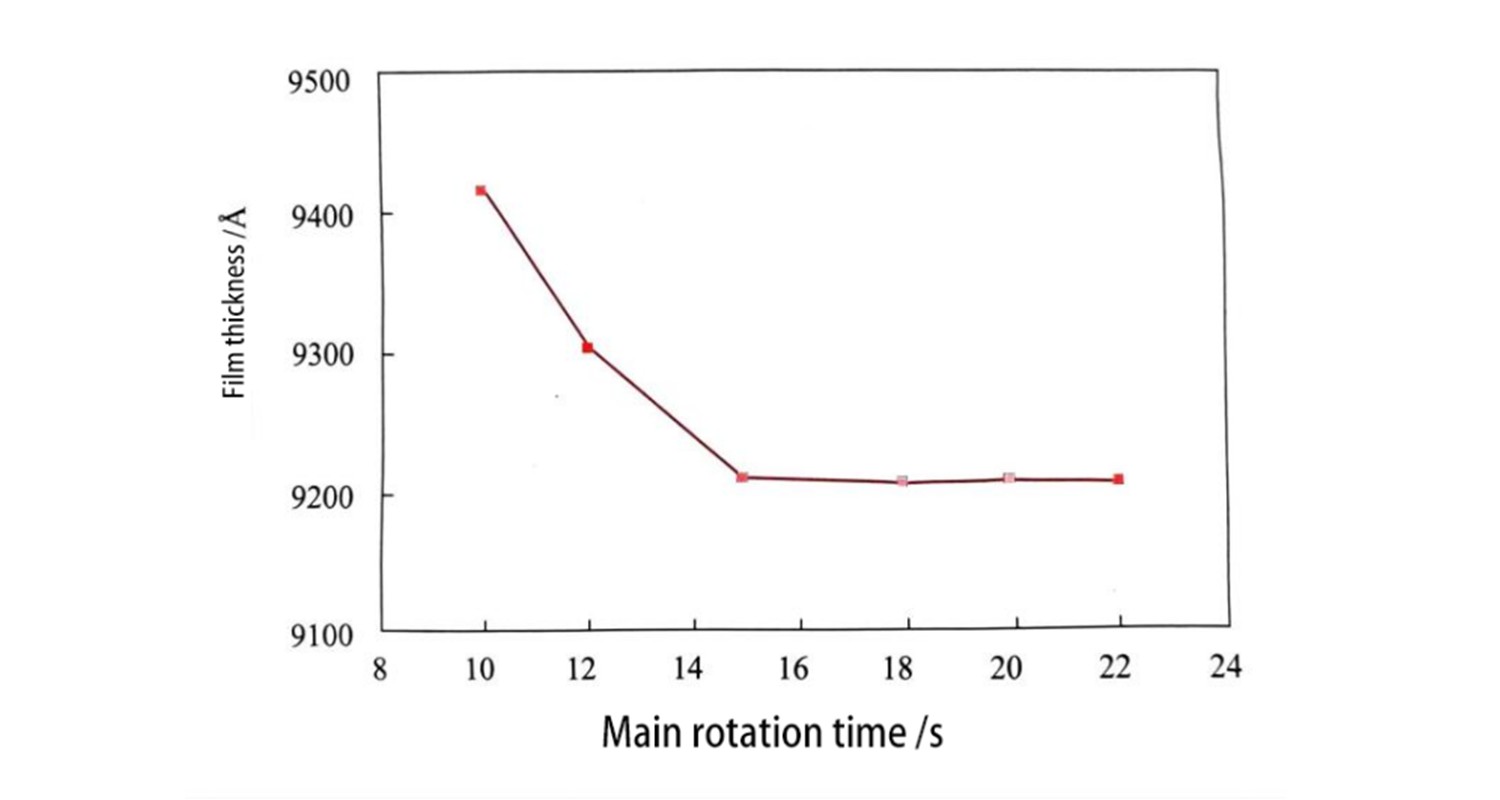
Figura 2: Relación entre el tiempo de rotación principal y el espesor de la película
Cuando el fotoprotector se gotea sobre el sustrato, incluso si la velocidad de rotación principal posterior es la misma, la velocidad de rotación del sustrato durante el goteo afectará el espesor final de la película. El espesor de la película fotoprotectora aumenta con el aumento de la velocidad de rotación del sustrato durante el goteo, lo que se debe a la influencia de la evaporación del disolvente cuando el fotoprotector se despliega después del goteo. La Figura 3 muestra la relación entre el espesor de la película y la velocidad de rotación principal a diferentes velocidades de rotación del sustrato durante el goteo del fotoprotector. Se puede ver en la figura que con el aumento de la velocidad de rotación del sustrato que gotea, el espesor de la película cambia más rápido y la diferencia es más obvia en el área con menor velocidad de rotación principal.
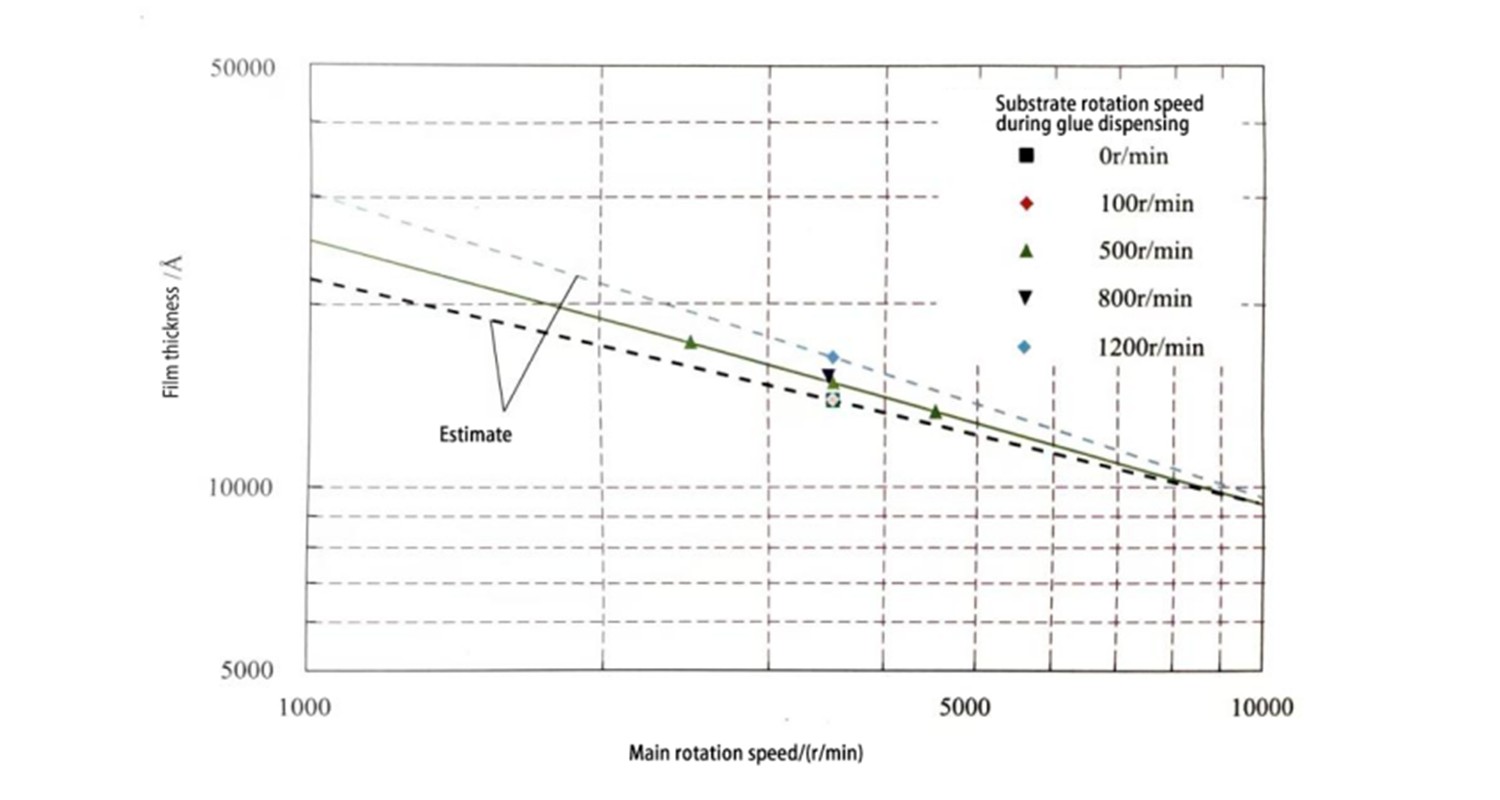
Figura 3: Relación entre el espesor de la película y la velocidad de rotación principal a diferentes velocidades de rotación del sustrato durante la dosificación del fotorresistente
Efecto de la humedad durante el recubrimiento.
Cuando la humedad disminuye, el espesor de la película aumenta, porque la disminución de la humedad promueve la evaporación del solvente. Sin embargo, la distribución del espesor de la película no cambia significativamente. La Figura 4 muestra la relación entre la humedad y la distribución del espesor de la película durante el recubrimiento.
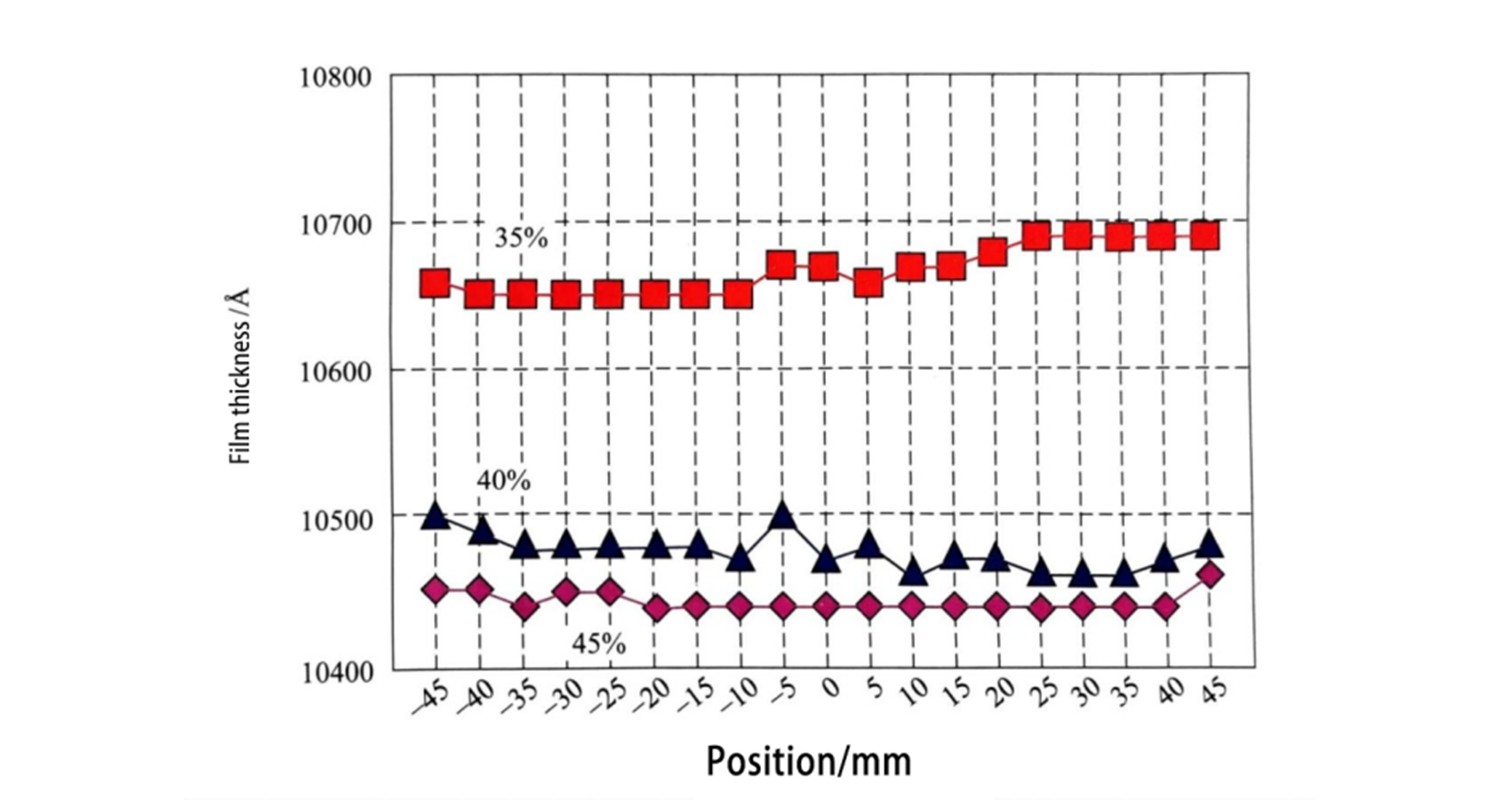
Figura 4: Relación entre la humedad y la distribución del espesor de la película durante el recubrimiento
Efecto de la temperatura durante el recubrimiento.
Cuando aumenta la temperatura interior, aumenta el espesor de la película. Puede verse en la Figura 5 que la distribución del espesor de la película fotorresistente cambia de convexa a cóncava. La curva de la figura también muestra que la mayor uniformidad se obtiene cuando la temperatura interior es de 26°C y la temperatura del fotorresistente es de 21°C.
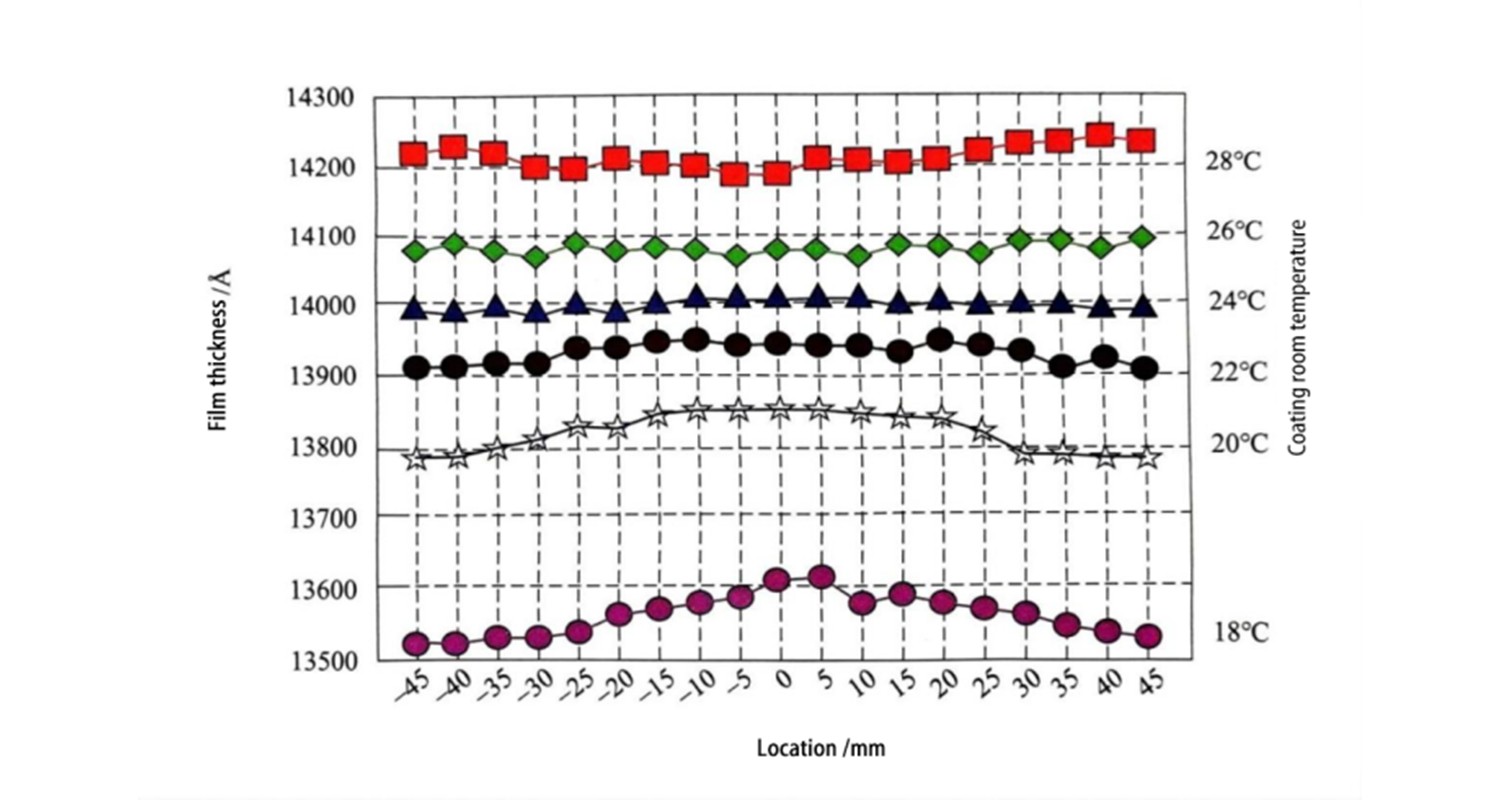
Figura 5: Relación entre la temperatura y la distribución del espesor de la película durante el recubrimiento
Efecto de la velocidad de escape durante el recubrimiento.
La Figura 6 muestra la relación entre la velocidad de escape y la distribución del espesor de la película. En ausencia de escape, se observa que el centro de la oblea tiende a espesarse. Aumentar la velocidad de escape mejorará la uniformidad, pero si se aumenta demasiado, la uniformidad disminuirá. Se puede observar que existe un valor óptimo para la velocidad de escape.
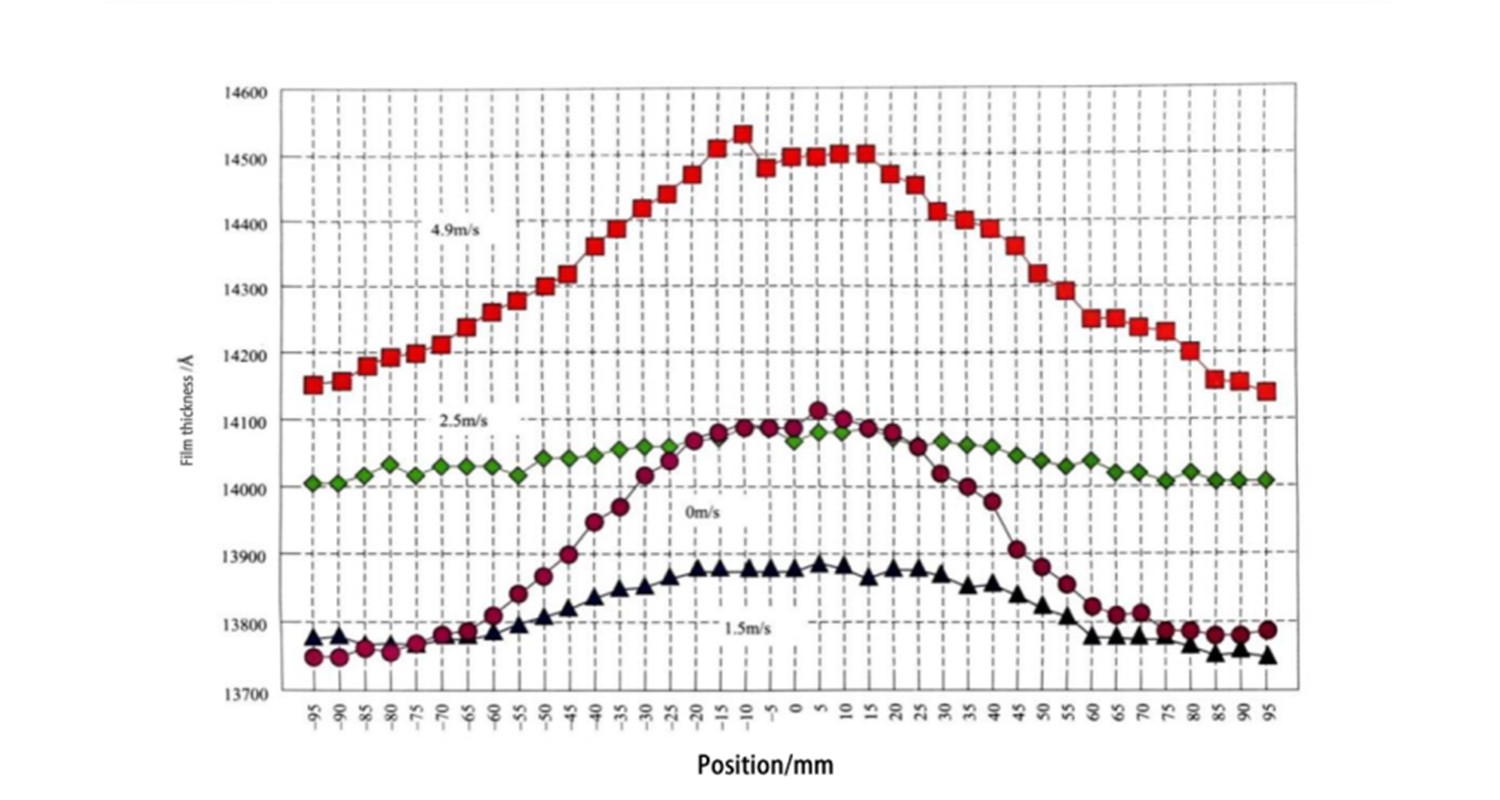
Figura 6: Relación entre la velocidad de escape y la distribución del espesor de la película
tratamiento HMDS
Para que el fotorresistente se pueda recubrir mejor, la oblea debe tratarse con hexametildisilazano (HMDS). Especialmente cuando se adhiere humedad a la superficie de la película de óxido de Si, se forma silanol, lo que reduce la adhesión del fotoprotector. Para eliminar la humedad y descomponer el silanol, la oblea generalmente se calienta a 100-120 °C y se introduce HMDS en niebla para provocar una reacción química. El mecanismo de reacción se muestra en la Figura 7. Mediante el tratamiento con HMDS, la superficie hidrófila con un ángulo de contacto pequeño se convierte en una superficie hidrófoba con un ángulo de contacto grande. Calentar la oblea puede obtener una mayor adhesión fotorresistente.
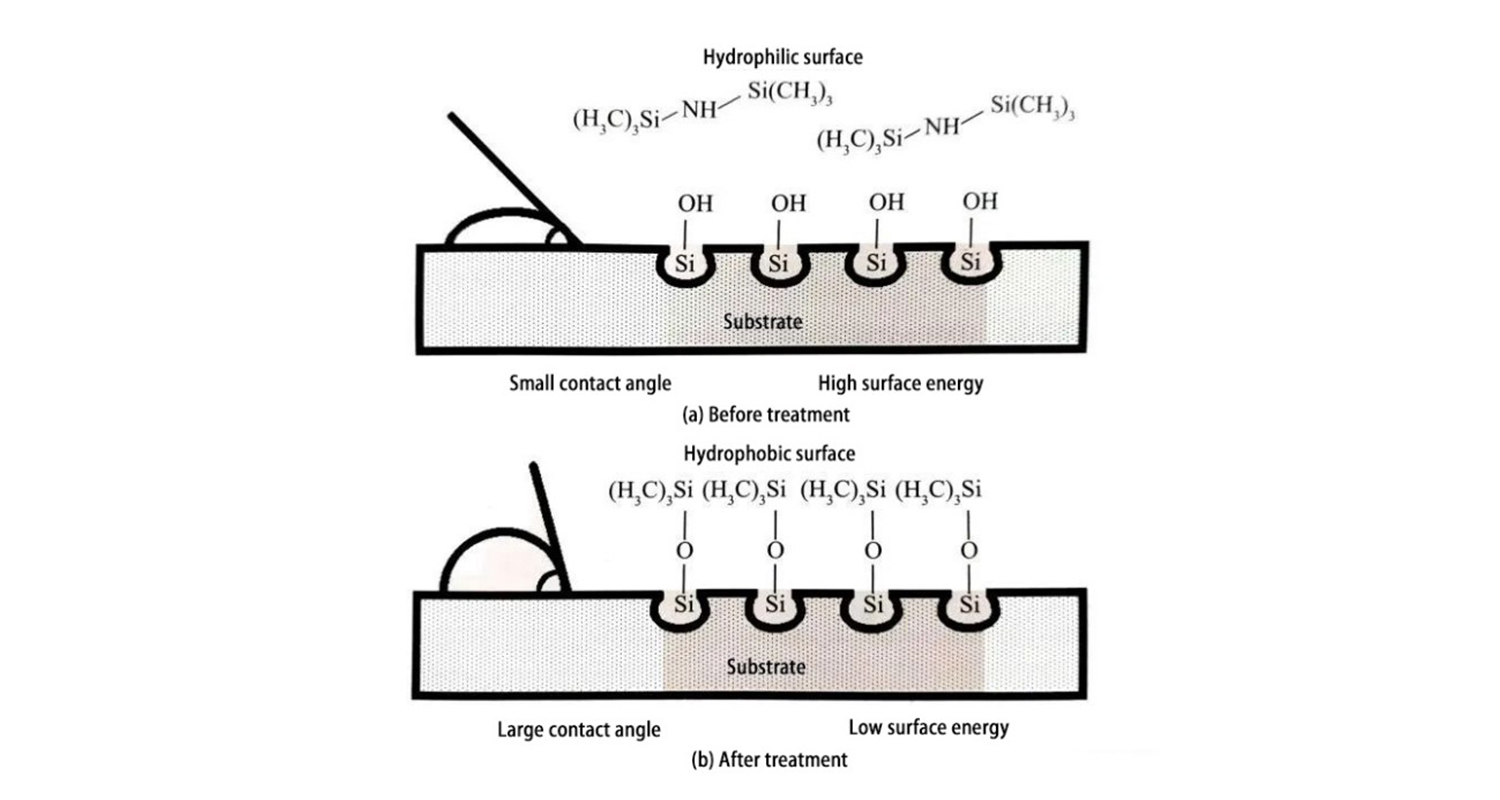
Figura 7: Mecanismo de reacción HMDS
El efecto del tratamiento con HMDS se puede observar midiendo el ángulo de contacto. La Figura 8 muestra la relación entre el tiempo de tratamiento con HMDS y el ángulo de contacto (temperatura de tratamiento 110 °C). El sustrato es Si, el tiempo de tratamiento con HMDS es superior a 1 minuto, el ángulo de contacto es superior a 80° y el efecto del tratamiento es estable. La Figura 9 muestra la relación entre la temperatura de tratamiento HMDS y el ángulo de contacto (tiempo de tratamiento 60 s). Cuando la temperatura supera los 120 ℃, el ángulo de contacto disminuye, lo que indica que el HMDS se descompone debido al calor. Por lo tanto, el tratamiento con HMDS generalmente se realiza entre 100 y 110 ℃.
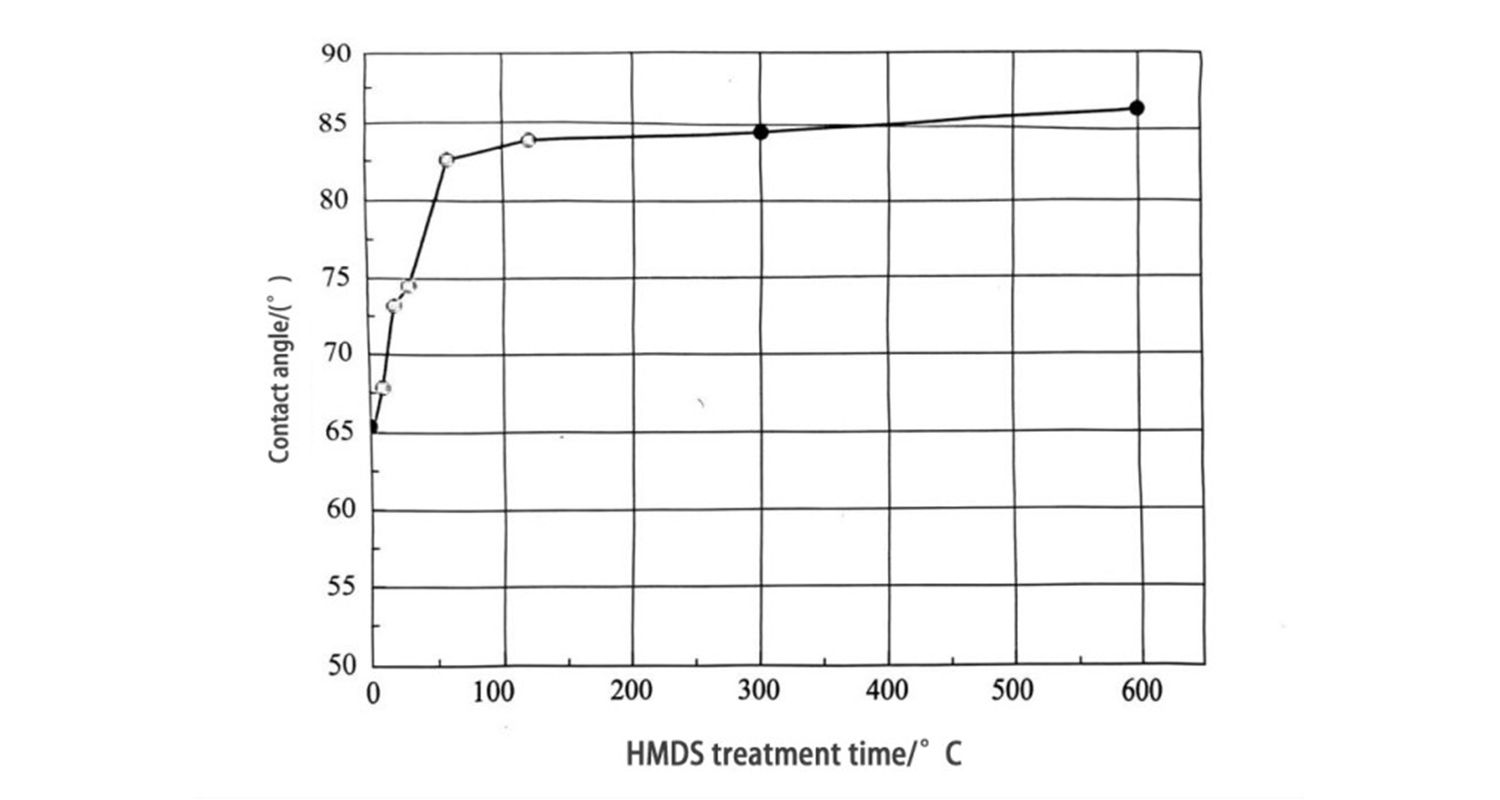
Figura 8: Relación entre el tiempo de tratamiento con HMDS
y ángulo de contacto (temperatura de tratamiento 110 ℃)
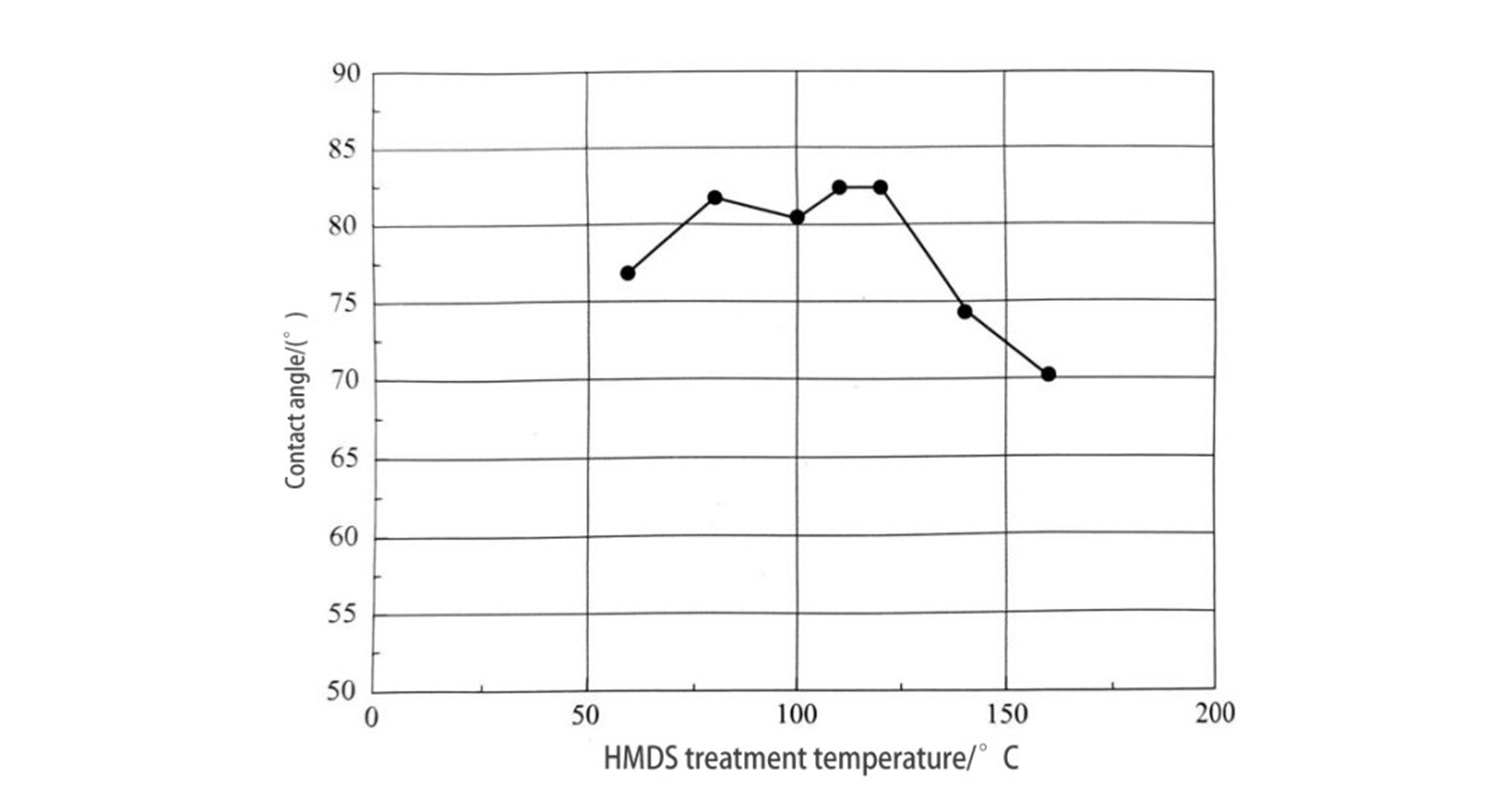
Figura 9: Relación entre la temperatura de tratamiento HMDS y el ángulo de contacto (tiempo de tratamiento 60 s)
El tratamiento HMDS se realiza sobre un sustrato de silicio con una película de óxido para formar un patrón fotorresistente. Luego se graba la película de óxido con ácido fluorhídrico añadiendo un tampón y se descubre que después del tratamiento con HMDS, se puede evitar que el patrón fotorresistente se caiga. La Figura 10 muestra el efecto del tratamiento con HMDS (el tamaño del patrón es de 1 um).
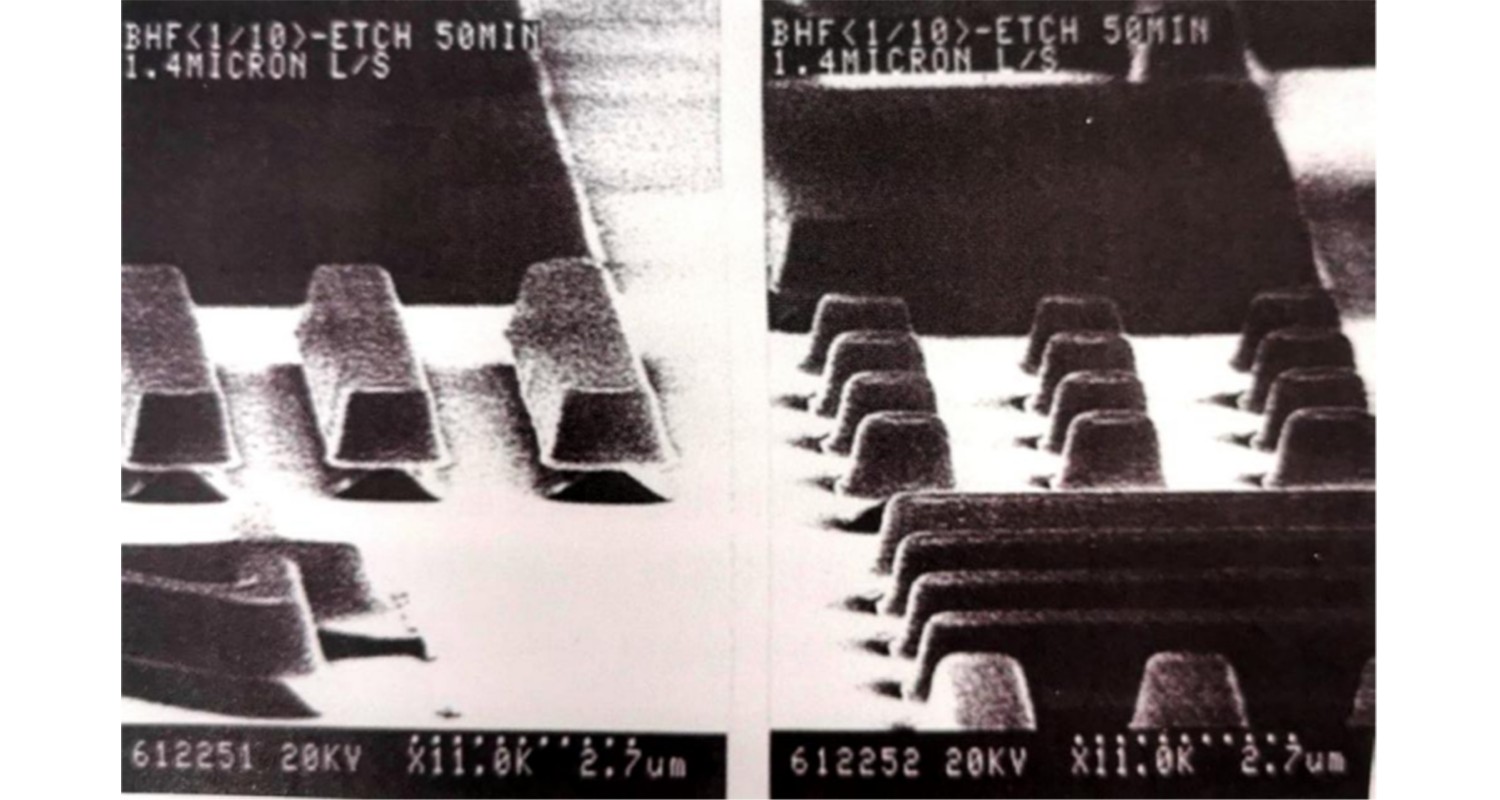
Figura 10: Efecto del tratamiento HMDS (el tamaño del patrón es 1 um)
precocido
A la misma velocidad de rotación, cuanto mayor es la temperatura de precocido, menor es el espesor de la película, lo que indica que cuanto mayor es la temperatura de precocido, más disolvente se evapora, lo que da como resultado un espesor de película más delgado. La Figura 11 muestra la relación entre la temperatura previa al horneado y el parámetro A de Eneldo. El parámetro A indica la concentración del agente fotosensible. Como puede verse en la figura, cuando la temperatura de precocción aumenta por encima de 140 °C, el parámetro A disminuye, lo que indica que el agente fotosensible se descompone a una temperatura superior a esta. La Figura 12 muestra la transmitancia espectral a diferentes temperaturas de prehorneado. A 160°C y 180°C, se puede observar un aumento en la transmitancia en el rango de longitud de onda de 300-500 nm. Esto confirma que el agente fotosensible se hornea y se descompone a altas temperaturas. La temperatura de precocción tiene un valor óptimo, que está determinado por las características de la luz y la sensibilidad.
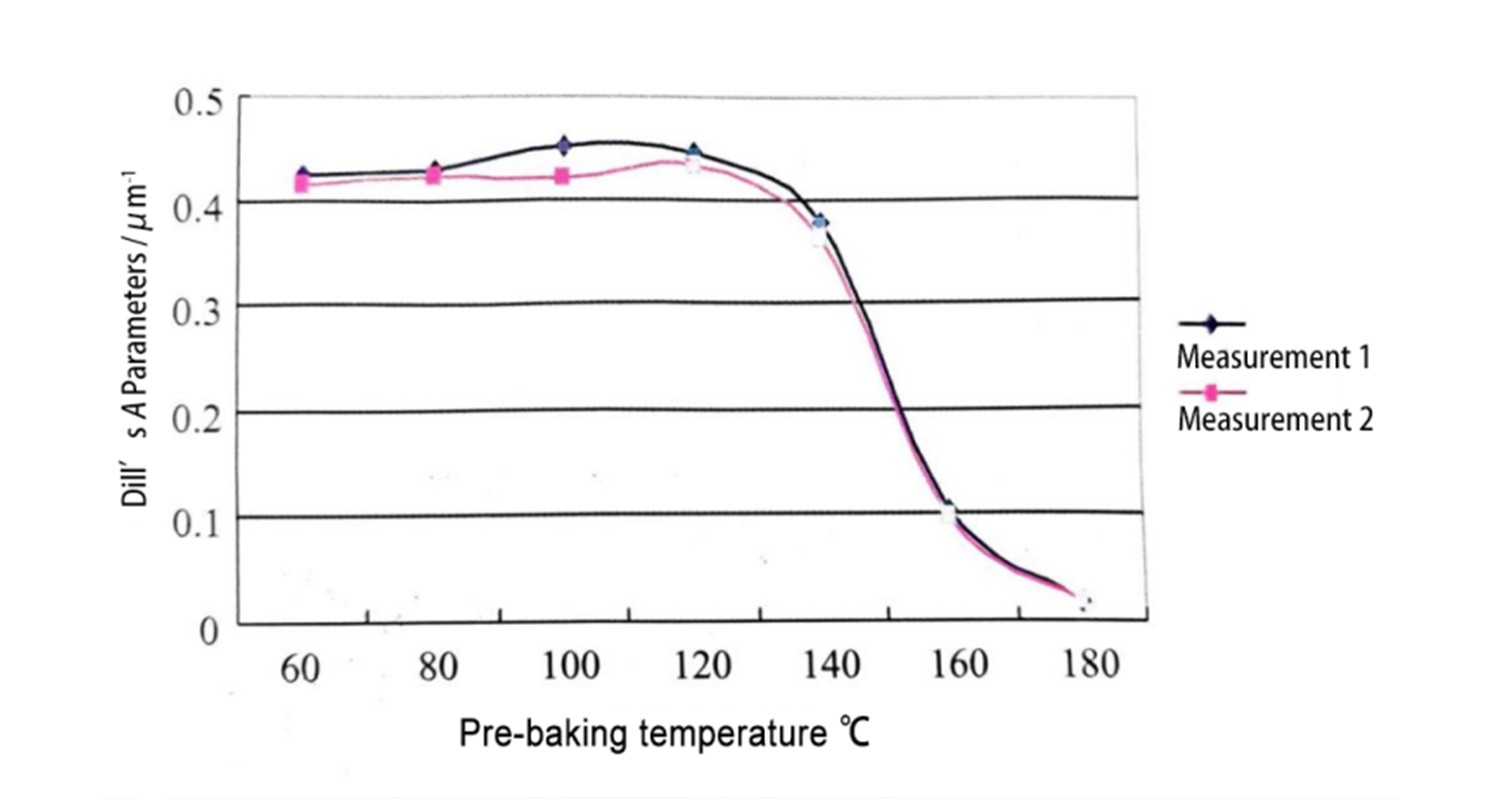
Figura 11: Relación entre la temperatura previa al horneado y el parámetro A de eneldo
(valor medido de OFPR-800/2)
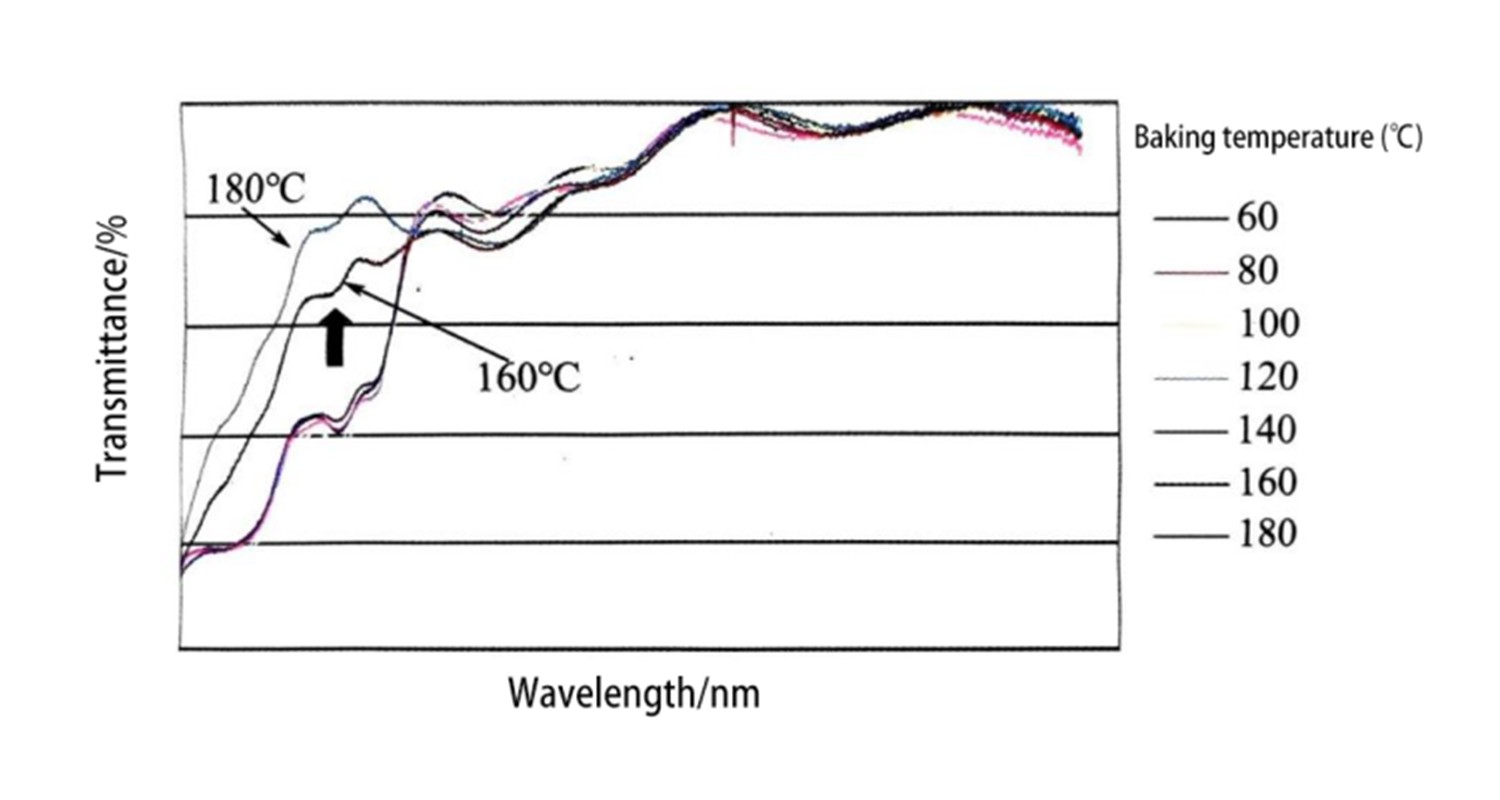
Figura 12: Transmitancia espectral a diferentes temperaturas previas al horneado
(OFPR-800, espesor de película de 1 um)
En resumen, el método de recubrimiento por rotación tiene ventajas únicas, como un control preciso del espesor de la película, un rendimiento de alto costo, condiciones de proceso suaves y una operación simple, por lo que tiene efectos significativos en la reducción de la contaminación, el ahorro de energía y la mejora del rendimiento de costos. En los últimos años, el spin-coat ha ido ganando cada vez más atención y su aplicación se ha extendido gradualmente a diversos campos.
Hora de publicación: 27 de noviembre de 2024